Slime drying machine Product Description
The slime itself is of high humidity and high cohesiveness. When traditional drying machine have failed to meet this requirement, the slime dryer uses a unique breaking device to disperse the bonded slime and dry it. The contact area between coal slime and hot air has been increased, so that the thermal efficiency has been greatly improved. After drying, the moisture of the slime reduces less than 12% at one time. The dried slime can be directly used as fuel, which make slime from waste into treasure.
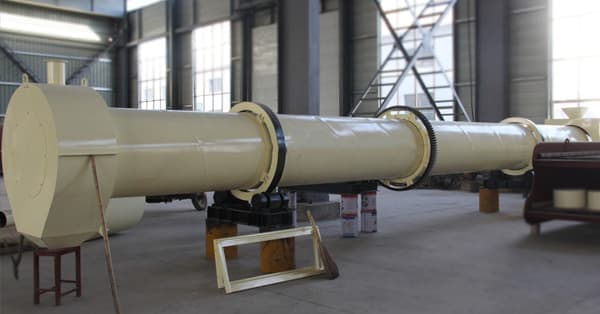
The slime drying system mainly consists of a heat source system (hot blast furnace, gas generator, boiling furnace), feeding system, conveying system, drying system, dust removal system, induced draft equipment, and electrical control system.
Slime drying machine Working Principle
The slime itself has high humidity and high cohesiveness. During the drying process, the wet coal slime enters the coal slurry disintegration equipment via a belt conveyor, and the rapidly-dispersed massive coal slurry enters the dryer with a negative pressure ,being divided into Four working areas: First, the feed area, where the wet coal slime enters and rapidly evaporates large amount of water after contact with hot wind of high temperature and negative pressure . The coal slurry is deformed under the large guide angle of the shovelling plate and then goes into the next working area;
Second, the cleaning area, the wet slime in this area is shovelled by the shovelling plate to form the material curtain, which is easy to form a sticking block on drum wall when falls down, due to the cleaning device, the slime can be rapidly cleaned out from the cylinder wall , thereby increasing the heat exchange area and the efficiency of heat and mass transfer to elate the drying rate; The third is the inclined plate area, which is a low-temperature drying area. The slime has been in a state of low moisture and looseness in this area,where has no adhesion phenomenon, After heat exchange, the finished product reaches the required moisture requirement, and enters the final discharging area.The fourth is discharge area, where has no shovelling plate any more, this material rolling to the discharge opening to complete the drying process.
Slime drying machine Features And Advantages
1.Strong anti-overload capability, large amount of processing capacity, low fuel consumption, and low drying cost;
2, Application of co-current drying method, the flue gas and wet materials are fed into the dryer from the same side , you can use high-temperature flue gas to obtain a high evaporation intensity, while the outlet temperature is low, which is to achieve high thermal efficiency;
3. The operating parameters can be changed according to the nature of different materials, so that the material can form a stable full-cut curtain in the cylinder body to achieve more fully heat exchange ;
4. The new feeding and discharging device eliminates plugging, discontinuity, inhomogeneity, and material returning , which reduces the load on the dust removal system.
5. The new internal structure strengthens the cleaning and heat conduction of the dispersed materials, eliminating the sticking phenomenon of the inner wall of the cylinder, and has stronger adaptability to moisture and viscosity of the materials;
6. The dryer achieves “zero horizontal thrust”, which greatly reduces the wear of the brace wheel and ensures smooth and reliable operation of the barrel.
7. Aadopting “aligning roller device” to make the contact between the rollers always linear, thus greatly reducing wear and power loss;
8. The product can control the particle size and moisture according to the user's requirements. When the slime is dried, the product moisture can reach below 8%, and the particle size can be controlled below 8mm.
Slime drying machine Technical Parameter
1. Drying of materials such as coal slurry, raw coal, flotation clean coal, and mixed clean coal in the coal industry;
2. Drying of blast furnace slag, clay, limestone, sand, quartz stone and other materials in the construction industry;
3.Drying of various metal concentrates, waste slag, tailings and other materials in the beneficiation industry;
4. Drying of non-thermosensitive materials in the chemical industry.
Model | Capacity(t/h) | Power(kw) | Reducer model | Feed water(%) | Fuel Calorific value | Water discharge(%)
|
φ1.2×10 | 2.5-3 | M160M-6 75 | ZQ350||-25 | 25±5 | ≥5500 | ≤13 |
φ1.5×14 | 7-9 | Y180L-6 15 | ZQ400||-31.5 | 25±5 | ≥5500 | ≤13 |
φ1.5×18 | 9.5-12 | Y180L-6 15 | ZQ400||-31.5 | 27±5 | ≥5500 | ≤13 |
φ1.8×14 | 12-15 | Y200L-6 18.5 | ZQ400||-31.5 | 25±5 | ≥5500 | ≤13 |
φ1.8×18 | 14-18 | Y200L1-6 18.5 | ZQ400||-31.5 | 27±5 | ≥5500 | ≤13 |
φ2.0×18 | 18-22 | Y200L2-6 22 | ZQ500||-31.5 | 25±5 | ≥5500 | ≤13 |
φ2.0×20 | 18-23 | Y200L2-6 22 | ZQ500||-31.5 | 30±5 | ≥5500 | ≤13 |
φ2.2×18 | 21-25 | Y200L2-6 22 | ZQ650||-31.5 | 27±5 | ≥5500 | ≤13 |
φ2.2×20 | 22-25 | Y225M-6 30 | ZQ650||-31.5 | 30±5 | ≥5500 | ≤13 |
φ2.4×20 | 25-29 | Y225M-6 30 | ZQ750||-31.5 | 27±5 | ≥5500 | ≤13 |
φ2.4×22 | 26-30 | Y225M-6 30 | ZQ750||-31.5 | 30±5 | ≥5500 | ≤13 |
φ2.6×20 | 28-33 | Y225M-6 37 | ZQ850||-31.5 | 25±5 | ≥5500 | ≤13 |
φ2.6×24 | 29-35 | Y225M-6 37 | ZQ850||-31.5 | 30±5 | ≥5500 | ≤13 |
φ3.0×20 | 45-50 | Y280S-6 | ZQ1000||-31.5 | 25±5 | ≥5500 | ≤13 |