Titanium Chrome Ore Rotary Kiln Product Description
Rotary kiln calcining kiln structure of titanium dioxide is similar to alumina,cement structure of titanium rotary kilnindustry,the cylinder is made of steel plate,the inner lining refractory lining,forming a predetermined angle with the horizontal line.
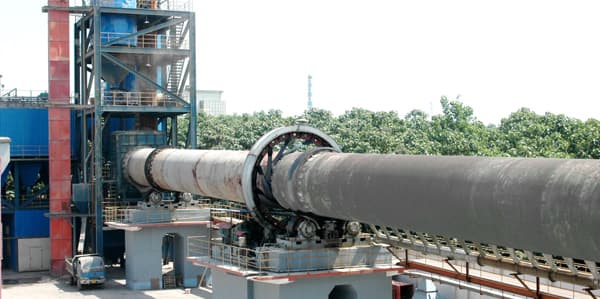
Cylinder sleeve has three pieces of rectangular wheel support in each file support device.In the middle belt near the cylinder with tangential spring plate fixed with a big gear ring,the 300 a small meshed gears.
During normal operation,the main drive motor through reducer to transfer power to the open gear driving device,rotary kiln.
Titanium Chrome Ore Rotary Kiln Working Principle
1. Crushing and milling,The dry crude material will be crushed and milled first.
2. Calcination:After milling, the materials would enter the kiln outlet( high end of the cylinder) through the preheater, and then are fed into the kiln by the tremie pipe. Meanwhile, The heating source is sprayed into kiln by burner barrel in the head of the kiln. Due to the inclination of the cylinder and slow rotation of the cylinder, the materials roll in hoop direction.
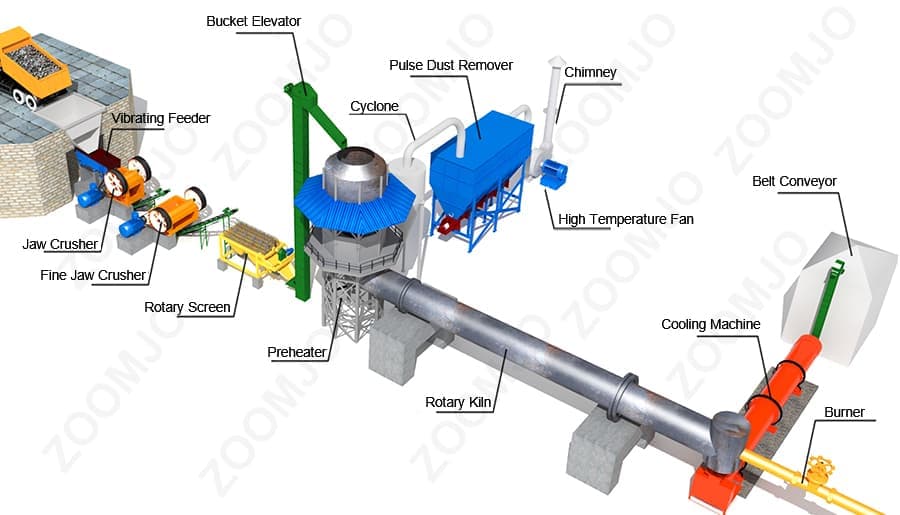
3.Cooling:Then the materials are discharged from the head of the kiln and enter the cooling device and be cooled.
4. Screening:Then they will go through the screens and final products will be conveyed to the yard. The big size materials will be sent back and processed.
Titanium Chrome Ore Rotary Kiln Features And Advantages
1. Simple structure;
2. Convenient and reliable control during the production process;
3. A few wearing parts;
4. High operation ratio.
Titanium Chrome Ore Rotary Kiln Technical Parameter
Specification (m) | Kiln Size | Power (kw) | Wight (t) | Remarks |
Diameter(m) | Length(m) | Slope(%) | Capacity (t/d) | Speed (r/min) |
Φ2.5×40 | 2.5 | 40 | 3.5 | 180 | 0.44-2.44 | 55 | 149.61 |
|
Φ2.5×50 | 2.5 | 50 | 3 | 200 | 0.62-1.86 | 55 | 187.37 |
|
Φ2.5×54 | 2.5 | 54 | 3.5 | 280 | 0.48-1.45 | 55 | 196.29 | Kiln decomposition kilns |
Φ2.7×42 | 2.7 | 42 | 3.5 | 320 | 0.10-1.52 | 55 | 198.5 | ------ |
Φ2.8×44 | 2.8 | 44 | 3.5 | 450 | 0.437-2.18 | 55 | 201.58 | Kiln decomposition kilns |
Φ3.0×45 | 3 | 45 | 3.5 | 500 | 0.5-2.47 | 75 | 201.94 | ------ |
Φ3.0×48 | 3 | 48 | 3.5 | 700 | 0.6-3.48 | 100 | 237 | Kiln decomposition kilns |
Φ3.0×60 | 3 | 60 | 4 | 800 | 0.3-2 | 100 | 310 | ------ |
Φ3.2×50 | 3.5 | 50 | 4 | 1000 | 0.6-3 | 125 | 278 | Kiln decomposition kilns |
Φ3.3×52 | 3.3 | 52 | 3.5 | 1300 | 0.266-2.66 | 125 | 283 | Preheating decomposition kilns |
Φ3.5×54 | 3.5 | 54 | 3.5 | 1500 | 0.55-3.4 | 220 | 363 | Preheating decomposition kilns |
Φ3.6×70 | 3.6 | 70 | 3.5 | 1800 | 0.25-1.25 | 125 | 419 | Waste heat power kilns |
Φ4.0×56 | 4 | 56 | 4 | 2300 | 0.41-4.07 | 315 | 456 | Preheating decomposition kilns |
Φ4.0×60 | 4 | 60 | 3.5 | 2500 | 0.396-3.96 | 315 | 510 | Preheating decomposition kilns |
Φ4.2×60 | 4.2 | 60 | 4 | 2750 | 0.41-4.07 | 375 | 633 | Preheating decomposition kilns |
Φ4.3×60 | 4.3 | 60 | 3.5 | 3200 | 0.396-3.96 | 375 | 583 | Preheating decomposition kilns |
Φ4.5×66 | 4.5 | 66 | 3.5 | 4000 | 0.41-4.1 | 560 | 710.4 | Preheating decomposition kilns |
Φ4.7×74 | 4.7 | 74 | 4 | 4500 | 0.35-4 | 630 | 849 | Preheating decomposition kilns |
Φ4.8×74 | 4.8 | 74 | 4 | 5000 | 0.396-3.96 | 630 | 899 | Preheating decomposition kilns |
Φ5.0×74 | 5 | 74 | 4 | 6000 | 0.35-4 | 710 | 944 | Preheating decomposition kilns |
Φ5.6×87 | 5.6 | 87 | 4 | 8000 | Max4.23 | 800 | 1265 | Preheating decomposition kilns |
Φ6.0×95 | 6 | 95 | 4 | 10000 | Max5 | 950×2 | 1659 | Preheating decomposition kilns |