Nickel laterite rotary kiln Product Description
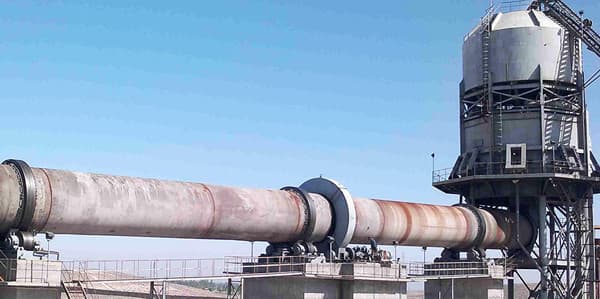
Raw material yard → screening, crushing and mixing dosing → rotary kiln → ore-heating furnace → iron ladle desulphurisation → refining converter → casting. On this basis, technologies such as pre-drying of raw materials, pelletizing of raw materials, energy saving and waste heat generation in rotary kilns, smelting in ore-heating furnaces and dosing of low melting point slag systems, the use of bottom-blowing or side-blowing refining converters instead of top-blowing converters, and nickel-iron granulation have been developed for plants with different conditions.
Nickel laterite rotary kiln Working Principle
The ore, limestone and reducing agent are screened and crushed in the raw material yard and preparation room and then mixed and fed into the rotary kiln.
In the nickel laterite rotary kiln, the raw material is dried, roasted and pre-reduced to produce a nickel slag at approx. 1000°C. The rotary kiln flue gas is discharged via a waste heat boiler, dust removal and desulphurisation, and the dust is mixed with the raw material and fed into the kiln again.
The nickel slag is added to the furnace silo (lined with refractory bricks) in a closed and insulated state (overhead feeding trolley) and distributed to the furnace by means of a discharge pipe in different positions according to the process requirements.
The furnace is fully enclosed, self-baking electrode, submerged arc smelting, reduction and fusion of crude ferro-nickel and slag, and at the same time produces about 75% of Co mine hot furnace barren gas, which is purified and sent to the rotary kiln burner, where it is used as fuel together with pulverised coal, and the dust removal ash is treated and returned to the raw material yard. The slag from the mining hot stove is water quenched and used as a building material for road construction and brick making.
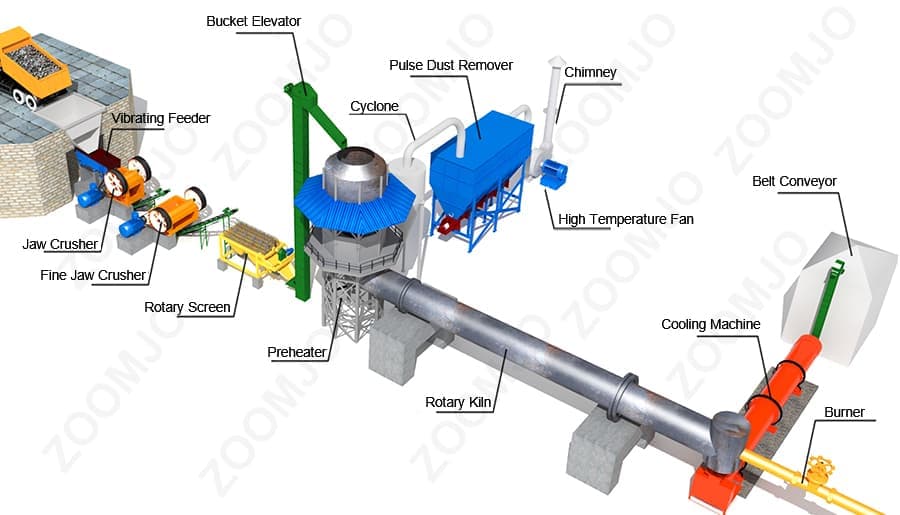
The product of the ore-heating furnace is crude ferro-nickel, before the iron out of the iron ladle plus desulphurisation agent, iron out of the same time desulphurisation, crude ferro-nickel containing Si, C, P and other impurities, the need to continue refining, slagging, into the acid converter, blowing oxygen desilicon, while adding nickel-containing waste to prevent high iron temperature, desilicon after slagging (or block slag iron), into the alkaline converter, blowing oxygen dephosphorisation, decarbonisation, while adding limestone to create alkaline slag. After the alkaline converter refining, the nickel ferrous water is sent to the pouring workshop and cast into qualified commercial nickel-iron blocks or made into granular nickel-iron.
Nickel laterite rotary kiln Features And Advantages
1. High adaptability of raw materials. Can be applied to magnesian silicate ores and limonite-type nickel oxide ores with iron content not higher than 30%, as well as intermediate type ores. Suitable for nickel oxide ores with high magnesium and low iron which are difficult to process using the wet process.
2. High nickel and iron grades with less harmful elements. For the same ore, the RKEF process produces a higher grade of ferronickel than the blast furnace process and the "sintered ore - hot mineral furnace" process. The desulphurisation and converter refining processes of the process can reduce the harmful elements of ferronickel to within the limits required by the ISO 6501 standard, which is welcomed by steelmaking users.
3. Energy saving and environmental protection, recycling. The raw material has more moisture and no dust is generated in the material yard and during the screening and crushing transportation process. The waste heat from the rotary kiln flue gas can be recovered for steam generation and discharged into the atmosphere after the flue gas desulphurisation meets the environmental requirements. The slag can be used for paving or making cement. From the water-containing charge into the rotary kiln until the iron out of the furnace slag in the whole process of production, the furnace is in a fully enclosed, environmentally friendly and energy-saving.
4. Nickel slag hot material into the ore-heating furnace. The nickel slag produced by the rotary kiln is fed into the furnace at a high temperature above 900°C, which saves a lot of physical and chemical heat, significantly reduces the consumption of electricity and reducing agent and improves the production efficiency compared to the cold material fed into the furnace of "sintering ore - mineral furnace".
Nickel laterite rotary kiln Technical Parameter
Specification (m) | Kiln Size | Power (kw) | Wight (t) | Remarks |
Diameter(m) | Length(m) | Slope(%) | Capacity (t/d) | Speed (r/min) |
Φ2.5×40 | 2.5 | 40 | 3.5 | 180 | 0.44-2.44 | 55 | 149.61 |
|
Φ2.5×50 | 2.5 | 50 | 3 | 200 | 0.62-1.86 | 55 | 187.37 |
|
Φ2.5×54 | 2.5 | 54 | 3.5 | 280 | 0.48-1.45 | 55 | 196.29 | Kiln decomposition kilns |
Φ2.7×42 | 2.7 | 42 | 3.5 | 320 | 0.10-1.52 | 55 | 198.5 | ------ |
Φ2.8×44 | 2.8 | 44 | 3.5 | 450 | 0.437-2.18 | 55 | 201.58 | Kiln decomposition kilns |
Φ3.0×45 | 3 | 45 | 3.5 | 500 | 0.5-2.47 | 75 | 201.94 | ------ |
Φ3.0×48 | 3 | 48 | 3.5 | 700 | 0.6-3.48 | 100 | 237 | Kiln decomposition kilns |
Φ3.0×60 | 3 | 60 | 4 | 800 | 0.3-2 | 100 | 310 | ------ |
Φ3.2×50 | 3.5 | 50 | 4 | 1000 | 0.6-3 | 125 | 278 | Kiln decomposition kilns |
Φ3.3×52 | 3.3 | 52 | 3.5 | 1300 | 0.266-2.66 | 125 | 283 | Preheating decomposition kilns |
Φ3.5×54 | 3.5 | 54 | 3.5 | 1500 | 0.55-3.4 | 220 | 363 | Preheating decomposition kilns |
Φ3.6×70 | 3.6 | 70 | 3.5 | 1800 | 0.25-1.25 | 125 | 419 | Waste heat power kilns |
Φ4.0×56 | 4 | 56 | 4 | 2300 | 0.41-4.07 | 315 | 456 | Preheating decomposition kilns |
Φ4.0×60 | 4 | 60 | 3.5 | 2500 | 0.396-3.96 | 315 | 510 | Preheating decomposition kilns |
Φ4.2×60 | 4.2 | 60 | 4 | 2750 | 0.41-4.07 | 375 | 633 | Preheating decomposition kilns |
Φ4.3×60 | 4.3 | 60 | 3.5 | 3200 | 0.396-3.96 | 375 | 583 | Preheating decomposition kilns |
Φ4.5×66 | 4.5 | 66 | 3.5 | 4000 | 0.41-4.1 | 560 | 710.4 | Preheating decomposition kilns |
Φ4.7×74 | 4.7 | 74 | 4 | 4500 | 0.35-4 | 630 | 849 | Preheating decomposition kilns |
Φ4.8×74 | 4.8 | 74 | 4 | 5000 | 0.396-3.96 | 630 | 899 | Preheating decomposition kilns |
Φ5.0×74 | 5 | 74 | 4 | 6000 | 0.35-4 | 710 | 944 | Preheating decomposition kilns |
Φ5.6×87 | 5.6 | 87 | 4 | 8000 | Max4.23 | 800 | 1265 | Preheating decomposition kilns |
Φ6.0×95 | 6 | 95 | 4 | 10000 | Max5 | 950×2 | 1659 | Preheating decomposition kilns |