Alumina rotary kiln Product Description
There are two types of rotary kilns used in alumina production. One kind resembles a firing kiln, where the material has physical and chemical changes in the kiln, with complex control and high working temperatures. The table is fed with a wet lance and is a wet kiln. There is another kind of kiln is only dehydration operation, will be attached to the aluminum hydroxide water and crystallization water in 1100 ℃ temperature conditions off, into powder alumina, this kiln is drying nature, become roasting kiln. These two types of kiln are basically identical in structure and work on the same principle.
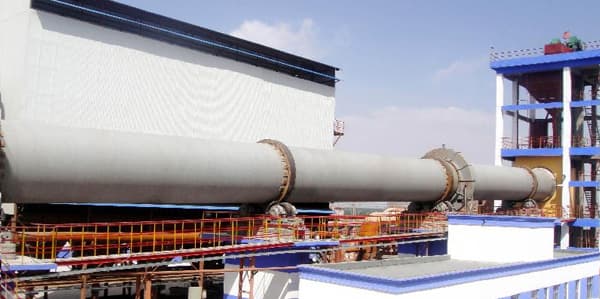
The rotary kiln is installed at a certain angle of inclination and the material moves continuously from the high end of the kiln to the low end. Its rotary speed and the size of the gear ring and sealing device all depend on the kiln diameter. This is why the decision on the kiln diameter is crucial. Its determination is mainly based on the results of thermal calculations. The length of the rotary kiln is determined firstly to ensure the completion of the reaction process in the kiln and secondly to take into account the amount of water vapour in the flue gas at the end of the kiln and to meet the requirements of the technical conditions of the point dust collection process.
Alumina rotary kiln Working Principle
The operation of a rotary kiln is, from the point of view of chemical unit operation, how to rationalise the heat and mass transfer process in the non-homogeneous phase of solid and gaseous media. The operation of such processes is technically demanding. There are many variables, so it is much more difficult to operate than the non-homogeneous heat and mass transfer process between gaseous and liquid media.
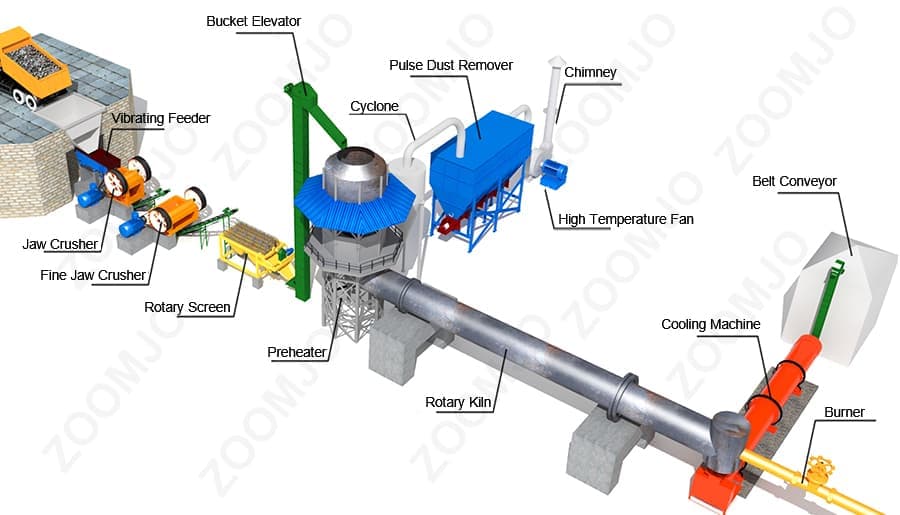
The rotary kiln is a rotary cylinder with a small angle of inclination to the horizontal line. When the cylinder is rotating, the material inside the cylinder moves gradually forward with the cylinder drive up and down the cylinder wall. The material is moving forward. When the material is in forward motion, it keeps on turning, and the gas in the kiln keeps on contacting with the new material turned up for non-homogeneous heat and mass transfer operation.
Alumina rotary kiln Features And Advantages
1、Reducing energy consumption
Alumina rotary kiln adopts bearing transmission, which greatly reduces electricity consumption and increases output by 50% and reduces energy consumption by 30% compared with the same grade of alumina rotary kiln.2、Wide application>Alumina rotary kiln is a kind of metallurgical chemical kiln, which can also be used in metallurgical industry for magnetization roasting of poor iron ore in iron and steel plants, oxidation roasting of chromium and nickel iron ore, roasting of high metallurgical ore in refractory plants and roasting of clinker in aluminum plants, aluminum hydroxide, and Chemical plant roasting chrome ore sand and chrome ore powder and other types of minerals.
3、Reliable operation
The alumina rotary kiln has a sturdy structure, smooth operation and high product quality, and can provide users with vertical preheater and five-stage cyclone preheater.
4、High output and low energy consumption
Alumina rotary kiln is easier to operate and more reliable than traditional equipment. Compared with the same specification equipment, the operation rate has increased by 10%, the output has increased by 5%-10% and the heat consumption has been reduced by 15%.
Alumina rotary kiln Technical Parameter
Specification (m) | Kiln Size | Power (kw) | Wight (t) | Remarks |
Diameter(m) | Length(m) | Slope(%) | Capacity (t/d) | Speed (r/min) |
Φ2.5×40 | 2.5 | 40 | 3.5 | 180 | 0.44-2.44 | 55 | 149.61 |
|
Φ2.5×50 | 2.5 | 50 | 3 | 200 | 0.62-1.86 | 55 | 187.37 |
|
Φ2.5×54 | 2.5 | 54 | 3.5 | 280 | 0.48-1.45 | 55 | 196.29 | Kiln decomposition kilns |
Φ2.7×42 | 2.7 | 42 | 3.5 | 320 | 0.10-1.52 | 55 | 198.5 | ------ |
Φ2.8×44 | 2.8 | 44 | 3.5 | 450 | 0.437-2.18 | 55 | 201.58 | Kiln decomposition kilns |
Φ3.0×45 | 3 | 45 | 3.5 | 500 | 0.5-2.47 | 75 | 201.94 | ------ |
Φ3.0×48 | 3 | 48 | 3.5 | 700 | 0.6-3.48 | 100 | 237 | Kiln decomposition kilns |
Φ3.0×60 | 3 | 60 | 4 | 800 | 0.3-2 | 100 | 310 | ------ |
Φ3.2×50 | 3.5 | 50 | 4 | 1000 | 0.6-3 | 125 | 278 | Kiln decomposition kilns |
Φ3.3×52 | 3.3 | 52 | 3.5 | 1300 | 0.266-2.66 | 125 | 283 | Preheating decomposition kilns |
Φ3.5×54 | 3.5 | 54 | 3.5 | 1500 | 0.55-3.4 | 220 | 363 | Preheating decomposition kilns |
Φ3.6×70 | 3.6 | 70 | 3.5 | 1800 | 0.25-1.25 | 125 | 419 | Waste heat power kilns |
Φ4.0×56 | 4 | 56 | 4 | 2300 | 0.41-4.07 | 315 | 456 | Preheating decomposition kilns |
Φ4.0×60 | 4 | 60 | 3.5 | 2500 | 0.396-3.96 | 315 | 510 | Preheating decomposition kilns |
Φ4.2×60 | 4.2 | 60 | 4 | 2750 | 0.41-4.07 | 375 | 633 | Preheating decomposition kilns |
Φ4.3×60 | 4.3 | 60 | 3.5 | 3200 | 0.396-3.96 | 375 | 583 | Preheating decomposition kilns |
Φ4.5×66 | 4.5 | 66 | 3.5 | 4000 | 0.41-4.1 | 560 | 710.4 | Preheating decomposition kilns |
Φ4.7×74 | 4.7 | 74 | 4 | 4500 | 0.35-4 | 630 | 849 | Preheating decomposition kilns |
Φ4.8×74 | 4.8 | 74 | 4 | 5000 | 0.396-3.96 | 630 | 899 | Preheating decomposition kilns |
Φ5.0×74 | 5 | 74 | 4 | 6000 | 0.35-4 | 710 | 944 | Preheating decomposition kilns |
Φ5.6×87 | 5.6 | 87 | 4 | 8000 | Max4.23 | 800 | 1265 | Preheating decomposition kilns |
Φ6.0×95 | 6 | 95 | 4 | 10000 | Max5 | 950×2 | 1659 | Preheating decomposition kilns |